Along the standby generator assembly line at Generac Power Systems Inc.’s Whitewater production facility, a robot swiftly puts the first pieces of a new unit in place before passing it along to employees who add other components.
Around the corner, a machine winds wires, freeing operators from a once-manual task so they can perform other work that requires a more human touch.
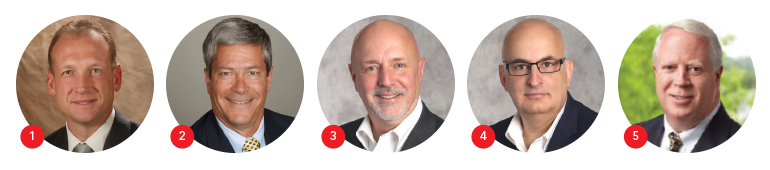
There are dozens of similar examples throughout the plant and thousands at manufacturers across the region. In addition to a $10 million facility expansion, Hartford-based Broan-NuTone LLC has invested $20 million in automation in recent years.
“Automation around here is a tool as much as a hammer or a wrench is,” said Paul Woelbing, president of Franklin-based Carma Laboratories Inc., the maker of Carmex.
Unlike in the past, when automation may have been a way to cut costs and eliminate positions, today’s manufacturers see it as a way to move their available workforce to other tasks and keep up with growth in an ever tightening labor environment.
“For us, it’s a very difficult workforce environment right now,” said Aaron Jagdfeld, chairman, president and chief executive officer of Waukesha-based Generac. “We’re much more focused on how do we take the workforce we have, hold on to them, develop them, maybe turn them into people who are operating automation equipment instead of actually assembling equipment.”
Jagdfeld and Woelbing will join Frank Carroll, chief executive officer of Broan-NuTone; Rich Simonson, Carma Laboratories chief operating officer and Keith Coursin, president of Germantown-based Desert Aire, at the 2018 Next Generation Manufacturing Summit. BizTimes Media and Milwaukee 7 are presenting the event, which will be hosted at Generac’s Waukesha headquarters on Oct. 4.
The rise of automation as a way to address labor shortfalls will be among the main topics of a panel discussion at the event. The executives will also discuss connecting their own leadership style to company strategy, the use of data within their organization, and managing through the current tumultuous tariff environment.
Increasing reliance on automation comes as Foxconn Technology Group continues work on site preparation for its $10 billion LCD manufacturing campus in Mount Pleasant. The company says it will employ 13,000 people when its plant is fully operational, potentially exacerbating the challenges of an already tight labor market.
“It will force us, like it will for other businesses in the area, to be more competitive in acquiring and retaining talent,” Simonson said.
The panelists all see Foxconn’s arrival as adding to the workforce challenge, but to differing degrees. For a company like Desert Aire, Coursin does not expect a direct pull for his company’s production workers. He does, however, see the potential for a chain reaction in which people living closer to the Foxconn site leave jobs at other companies to join the Taiwanese tech giant. New employees for the then-vacant positions at those employers could potentially come from areas, like Waukesha County, from which Desert Aire currently draws its employees, Coursin said. Companies located in the region’s northern counties, like Desert Aire in Washington County, might not be directly affected by Foxconn, but that chain reaction in the region’s labor market will impact everyone, he said.
“This is not going to be easy for anybody,” Carroll said. “I think there’s going to be challenges for all the manufacturers.”
Whether the workforce challenges are caused by Foxconn or existing demographic trends, many manufacturers are paying plenty of attention to where their workers will come from.
Carroll said Broan-NuTone is offering incentives to employees for referrals, continually reviewing wage structures and expanding co-op programs with area high schools.
Desert Aire has found a four-day workweek and some flexibility in start times has helped attract employees, particularly from younger generations.
Generac has invested heavily in its headquarters, recognizing that a location in western Waukesha County means better facilities are needed to overcome a longer commute in some cases. The company regularly holds walk-up interview days and Jagdfeld said it has also moved from hiring people for entry-level roles to hiring for early career paths. That means accelerating mentoring programs and giving employees the chance to change their direction within Generac.
“We can give you a lot of different experiences under the same umbrella,” he said. “We want to round you out because that actually makes you more valuable to us, as well.”
Simonson said addressing workforce challenges is about more than just attracting new employees; it is about holding on to the employees a company has.
“I think it’s about recognizing what motivates different individuals and trying to embrace that,” he said, noting many older employees are seeking security, transparency and an opportunity for later career advancement, while younger employees often seek flexibility and an opportunity to be part of something bigger than themselves.
Carma Labs has found success by being willing to pay up front for employees to pursue extra education or training instead of reimbursing after the fact, Simonson said.
“I think it’s a matter of having empathy for the people you work with,” Woelbing said.
Whether companies have solved their workforce challenges or not, the daily task of fulfilling orders and meeting customer needs continues. Many firms are increasingly turning to data to help them find business opportunities in production and in sales.
For Generac, that means making investments to add employees who understand data analytics and have worked at brands like MillerCoors LLC. Today, the company can use data on power outages, generator activations and other sources so that when there are 130,000 people without power in Michigan, for example, Generac has business rules for how to market to those people in targeted ways.
“For us, our math has always been about the calculations to design products,” Jagdfeld said. “This is almost like deep math around marketing, which is a totally different way of thinking about our business.”
Carma Labs has gone through a similar journey, converting from a focus on manufacturing to embracing Carmex as a brand and seeking to promote it.
“We didn’t know as much as we thought we knew,” Simonson said of the company’s data gathering and analysis efforts.
Carroll said Broan-NuTone is increasingly turning to data to help manage the company, but acknowledged there are members of leadership that are not entirely comfortable with it.
“We’re trying to get them into the everyday data and the numbers,” he said.
Even for Desert Aire, which makes custom dehumidifiers and can see one project on the shop floor for weeks, data plays a key role. Coursin said the company tracks the amount of time spent on individual processes and even though some of the collection is more manual than he would like, it is a worthwhile endeavor.
“There’s a feedback component that keeps us going,” he said, noting the data provides insight into which employees might need help or training and which are exceeding expectations and should be compensated accordingly.
Data and automation both have the potential to help manufacturers improve operations, but they can also cause concerns for employees, whether it is in job security or just a change in the way of doing things. The panelists all emphasized the importance of transparency with employees in implementing new technology.
“We are looking at automation in every step to maintain our U.S. footprint,” Carroll said.
Coursin added that companies have to develop a plan for how they are going to invest.
“Technology is not inexpensive, so you literally have to allocate and say, ‘We’re going to do this project this year,’” he said. “I’d love to have an infinite amount of time and resources to implement some of this stuff.”