Employees working side-by-side with nimble collaborative robots is becoming more common on factory floors at manufacturers of all sizes, especially as a means of overcoming challenges tied to an increasingly troublesome labor shortage plaguing the industrial sector.
“We’ve made the robots attractive to almost everybody,” says Matt Fitzgerald, Vice President of Product at Rethink Robotics Inc., a Boston-based maker of collaborative robots and corresponding software.
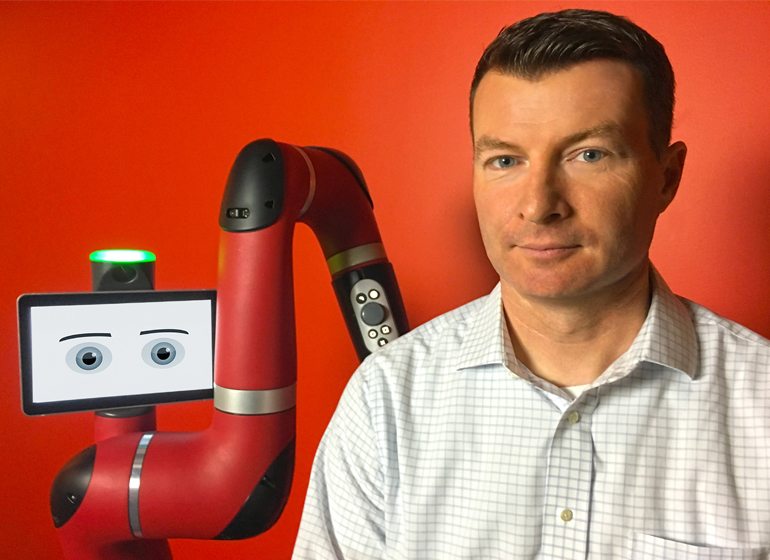
More than 1.7 million new industrial robots will be installed in factories around the world by 2020, according to the 2017 World Robotics Report conducted by the International Federation of Robotics.
The popularity of collaborative robots is being driven, in part, by their relatively low costs and ease of use, Fitzgerald says.
“It’s all visual programming. That really removes the intimidation of robots,” Fitzgerald said.
Fitzgerald will deliver the keynote address at the Wisconsin Manufacturing Extension Partnership’s Manufacturing Matters! conference on March 1 at the Hyatt Regency Hotel in Milwaukee.
Robotics, once thought to be unattainable for small and mid-size manufacturers, have become much more affordable. Prices for Rethink Robotics’ collaborative robots start at $35,000.
Rethink Robotics launched in 2008 under the direction of co-founders Rodney Brooks, a professor who headed the computer science and artificial intelligence lab at the Massachusetts Institute of Technology, and Ann Whittaker, who has held various management roles at MIT. Brooks previously co-founded iRobot, a Bedford, Massachusetts-based consumer robot company best known for developing robots for home cleaning, including the Roomba vacuuming robots and the Braava family of mopping robots.
Rethink Robotics’ innovations have included the robot Baxter, released in 2012. Sawyer, introduced in 2015, is designed to perform more precise and detailed tasks.
Fitzgerald has been a member of the Rethink Robotics team since 2012 and has been integral in launching both the Sawyer and Baxter collaborative robots and leading the company’s product management team.
In the past, robots in industrial settings presented potential dangers and could be difficult to use, he says.
“Our robots are easy to use and intuitive. Most anybody can understand them and get them up and running quickly,” Fitzgerald said.
Collaborative robots can have an immediate and direct impact on manufacturers struggling to fill open jobs amidst low unemployment and dramatically changing demographics that are shrinking the workforce, Fitzgerald insists.
“Robots can do jobs on the line that manufacturers can’t find people to fill,” he says. “This labor shortage, the body gap, is a challenge not only in the United States but worldwide. Collaborative robots can fill that void.”
The use of robotics can also boost productivity, allowing for crucial increases in throughput, Fitzgerald says.
Fitzgerald acknowledges that issues have been raised about robots replacing workers and reducing the overall number of factory jobs.
“But if you look at the data, the labor shortage is real,” he says. “It’s also really hard for someone to do the same mundane, repetitive tasks for eight to 10 hours a day. Let workers use their talent and insight to do higher value tasks around the plant.”
Fitzgerald insists that collaborative robots have become safer, in part, through limits on power and force. The robots are designed to immediately stop when they detect any sort of potential collision with a worker or something in the immediate area.
“They’re specifically designed to work alongside people,” Fitzgerald said.
Collaborative robots offer advantages and affordability for small and mid-size manufacturers that may have been out of reach in the past.
Workers can expand their on-the-job skill sets by working with robots while also freeing them to do more challenging and rewarding work, Fitzgerald says.
Collaborative robots tie in well with the Internet of Things, an interconnection, via the Internet, of computing devices embedded in objects that enables them to send and receive data.
“Our robots are big bundles of sensors,” Fitzgerald says. “Sawyer has an embedded camera in the robot for locating parts before picking or placing. You can track cycle time and how much force was used when placing something into a fixture. It can tell you the run-time hours and the parts count. It can track all this data and send it out to be analyzed.”
Rethink Robotics plans to continue to grow its family of robots while developing leading-edge software.
“I think some of things we can look for in the future is how do we reduce the friction of integration with existing machinery and components in the work cell,” Fitzgerald says. “How can we continue to make it easier and faster for the robot to get set up, whether you are integrating with a programmable logic controller or a manufacturing execution system.”