Early career
One to 10 years of experience
Andy Wachholz is a student in his third year in mechanical engineering at Waukesha County Technical College. His junior year of high school, Andy wanted to start on his technical degree but also wanted to work to apply what he was learning and earn money for school. His school district partnered with GPS Education Partners Inc. to develop a specialized program for him.
He was enrolled as a Youth Apprentice at Generac Power Systems Inc. and completed his academic requirements to graduate high school at the GPS education center at Generac. He also took classes at WCTC and the University of Wisconsin-Waukesha through Wisconsin’s Youth/Course Options program to make progress on his post-secondary degree.
He graduated high school with his class at New Berlin West High School in 2016 as a level-two apprentice with a production technician certification. Andy is now working at Ritter Technology LLC while taking classes concurrently at UWM and WCTC. At work, he fixes broken hydraulic hoses, inspects parts, receives inventory and pulls orders.
“I am planning on a career in mechanical engineering. Ritter has an engineering department, so I will sit with the engineers in a few weeks to see if I like it,” Andy said. “I wanted to get into a career right away and not work weekends. Almost all my weekends are off. I have not worked a weekend in my life.”
For more information on GPS Education Partners, visit http://gpsed.org.
5 Tech Areas of Study in High Demand
You may not have considered these fields, but these areas of academic study will cover the skills required for key positions needed for today’s and tomorrow’s manufacturing workforce.
Automation (robotics)
Robotics technicians apply basic engineering principles and technical skills in support of engineers and other professionals engaged in developing, installing, calibrating, modifying and maintaining automated systems. This includes using computer systems; electronics and instrumentation; programmable logic controllers; electric, hydraulic and pneumatic control systems; actuator and sensor systems; process controls; applications to specific industrial tasks; and report preparation.
Industrial maintenance technology
Maintenance mechanics, millwrights and machine repairers fabricate, install, dismantle or move machinery and heavy equipment according to layout plans, blueprints or other drawings.
Duties may involve pipefitting; boiler making; insulating; welding; machining; carpentry; repairing electrical or mechanical equipment; installing, aligning and balancing new equipment; and repairing buildings, floors and stairs.
Metal fabrication & welding
Skills necessary for this field include:
- Attention to detail to perform precision work, often with straight edges and minimal flaws.
- Manual dexterity to hold equipment in place and move it precisely.
- Physical stamina to endure long periods of standing and repetitious movements.
- Spatial orientation to interpret two- and three-dimensional diagrams in order to fit metal products correctly.
Tool & die making
Die makers construct metal forms (dies) to shape metal in stamping and forging operations. Toolmakers analyze specifications, lay out metal stock, set up and operate machine tools, and fit and assemble parts to make and repair dies, gauges, jigs, fixtures (devices that hold metal while it is shaped, stamped or drilled), and machinist’s hand tools.
Automotive tech
Whatever his or her specialty, a technician’s key responsibility is diagnosing and fixing automotive problems. The technician uses precision tools, electronic diagnostic tools, and his or her training and skill to locate the cause of the problem. Once the cause is found, the technician makes adjustments or repairs. Technicians also perform routine maintenance on vehicles, such as oil changes and tune-ups. ν
(Sources: DWD, WCTC & Career Cruising)
GE Healthcare, Waukesha
Josephine Morrison (Josey) is senior technical product manager within the digital business of GE Healthcare and has four years of experience. GE Healthcare’s imaging and clinical care practice is headquartered in Wisconsin, where the largest concentration of GE Healthcare’s workforce – 6,000 employees – is located.
Josey graduated college and started in the GE Healthcare Digital Technology Leadership Program in the summer of 2013. She is part of IT manufacturing, which takes advantage of technologies and requires a workforce with STEM skills.
Josey’s advice to job seekers is, “Start early getting exposure to different careers and work functions. It helps you figure out what you like and what you don’t, which will make career choices easier in the future. Even take different classes to explore potential areas of interest.”
“Key skills are the ability to change and be flexible, which are important capabilities to have to work in any company,” Josey said. “Secondarily, I would say strong communications skills and being comfortable with technology helps. I was always interested in technology, math and problem solving.”
About working at GE, Josey said, “GE is an amazing company on the forefront of new technologies and products that will help people around the world. I am part of a new dynamic that is changing the culture of manufacturing. Who wouldn’t want to work here?”
GE Healthcare – Possible career tracks
Any one position in GE Healthcare can have numerous career tracks. Here are two examples in Josey’s area.
Product Management:
- Executive, product and analytics
- Senior product management
- Staff manager
- Product management manager
Technical product management – people leadership:
- Vice president
- Senior director
- Director
- Senior manager
- Manager
CAREER SNAPSHOT: Mechanical Engineer
One of the top jobs available now and in the future will be in mechanical engineering. Here’s a quick look at some of the details.
WHAT DO MECHANICAL ENGINEERS DO?
Mechanical engineers produce specifications for, design, develop, manufacture and install new or modified machines and mechanical components or systems.
WHAT SKILLS ARE REQUIRED?
Mechanical engineers need to be technically minded, able to demonstrate numerical and scientific ability, and have problem-solving skills. Engineers are creative, inquisitive, analytical and detail-oriented. They should be able to communicate well, both orally and in writing. The ability to work as part of a team is also important. Mechanical engineers have to keep up on new technology in their field and take courses.
WHERE DO THEY WORK?
Mechanical engineers work mostly in the manufacturing industry for firms that produce everything from transportation equipment to computer and electronic products. Some work in the utilities industry. Others may work for architectural companies or government agencies, and some work as independent consultants. Much of their time is spent in front of computer screens or meeting with accountants, advertisers or other businesspeople. They may also work on the factory floor with machinists, technicians and assemblers.
WHAT SCHOOLING IS REQUIRED?
A bachelor’s degree in mechanical engineering is usually the minimum educational requirement to work in this field. However, a degree in a closely related discipline, such as electrical engineering, may be acceptable as well. A master’s degree or a doctorate may be required for more senior positions or for advanced research and development jobs.
HOW MUCH DO THEY MAKE?
Most mechanical engineers earn between $52,000 and $122,000 a year, with an annual median of around $81,000. The highest salaries tend to be reserved for design specialists and those who have reached the level of supervisor or manager. Some senior engineers earn more than $125,000 a year.
(Source: Career Cruising)
Dual Enrollment Academy
Noah Evans was a New Berlin West student who wanted his coursework to lead to something after high school. He became a Dual Enrollment Academy welding student as a senior during the 2015-2016 school year.
In this program, he attended high school part time and worked toward his associate’s degree at Waukesha County Technical College. He earned three industry certifications in welding and metal fabrication. He graduated from high school in 2016, and was awarded technical honors in engineering.
Noah will be completing his associate degree in welding fabrication at WCTC in December. He is working for ACRO Automation Systems Inc. building robotic cells. His company will help him continue his education in welding.
For students in the Dual Enrollment Academy, costs are shared among WCTC, some industry sponsors and the school districts. With dual enrollment, young adults are getting into tech coursework earlier, finishing schoolwork sooner and more cheaply, and getting employed faster.
More information on Dual Enrollment Academy can be found here: https://www.wctc.edu/dual-enroll
Mid-career
10 to 20 years of experience
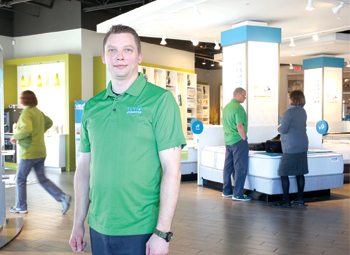
Adam Terasek, national service leader at Verlo, just celebrated his 15-year anniversary with the company and has found great success since he started building mattresses back in 2002. Adam cites patience, hard work and communication skills for his many promotions throughout the years.
For those considering a career in manufacturing or trade, Adam believes that “success means doing the right thing when no one is looking.” Another important skill? Communication. “Being in someone else’s home, I realized how important it was to interact with people and make customers feel comfortable. Those communication skills have come a long way in my career.”
Adam’s career ladder:
- Mattress Builder: After high school, Adam started his career assembling up to 45 mattress foundations a day in Verlo’s Greenfield manufacturing location. In this role, he also built and sewed mattresses to guests’ specifications.
- Delivery Assistant/Lead Delivery: In these delivery roles, Adam managed the products entering the warehouse, completed delivery and set-up of mattresses and interacted with customers in their homes when delivering the mattress.
- Warehouse Manager: As a warehouse manager, Adam managed inventory, product flow process, and ensured all deliveries went out in a timely, efficient manner.
- Comfort Coach/Senior Comfort Coach: In this position, Adam helped guests learn about mattresses and which mattress was the right purchase for them. As a senior comfort coach, Adam trained new employees with a newly created training program.
- Store Manager: As the store manager, Adam was responsible for an entire Verlo store and ensuring the store was profitable. This included managing his employees and store inventory.
- National Service Leader: Now, as the national service leader, Adam manages concerns and inquiries from customers all around the country. He also works with the owners of Verlo’s 37 national stores to resolve customer service issues.
CNH Industrial, Racine
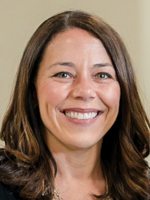
Amy Hall, manager of change management, world class finance, has 14 years of experience working for CNH Industrial, a global manufacturer of agricultural and construction equipment, industrial engines and commercial vehicles.
A Midwest native, Amy was a temporary employee for about a year and then transitioned to a full-time staff position in the finance department at CNH.
“I had great managers – it was not important to them that I did not have a business or finance background, because (through my work) I showed I had the skillset to learn,” Amy said. Since then, Amy has held several managerial positions and earned a master’s degree in business administration.
Amy traveled to CNH Industrial’s manufacturing plants across the United States and internationally. Those visits gave her the opportunity to see how raw materials are turned into equipment the company sells.
No day is the same for Amy in her current role as change management manager. She works on multiple projects, both internally with CNH employees, and externally with retail dealers. Additionally, Amy leads a talent development program for recent college graduates.
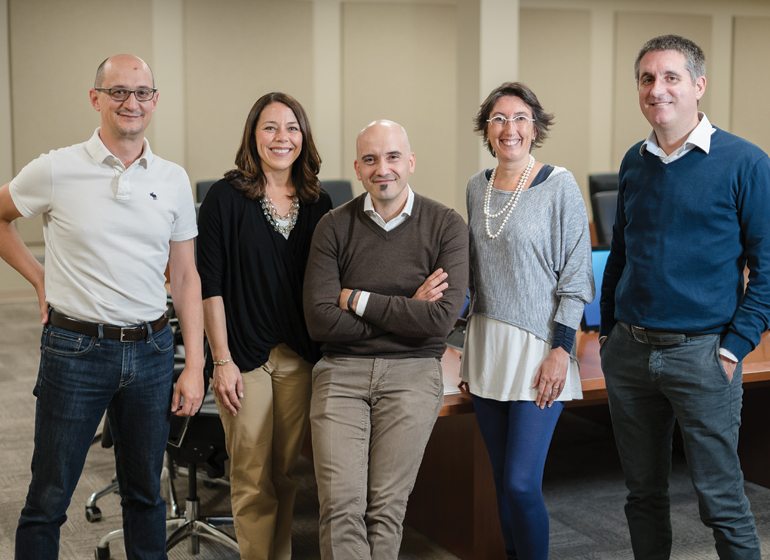
In terms of career decisions, Amy advises students to focus on an area that they are passionate about, then decide on an industry sector to join – for her it became manufacturing. “We are a huge global company with so many divisions or functional areas. No matter what your interest might be, there is a place for you in the company,” Amy said.
Amy’s positions & education
Positions
- Customer service associate
- Aftermarket project specialist
- Manager of quality control
- Manager, internal controls & processes
- Accounts payable manager
- Finance talent development program coordinator
Education and certificates
- Alverno College | Milwaukee – M.A., business administration
- Macalester College | St. Paul, MN – B.A., anthropology
- University of Wisconsin-Milwaukee – certificate in office lean
- Prosci certified change practitioner
GE Healthcare, Waukesha
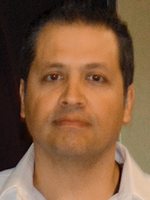
In only 17 years, Zeferino Cisneros (Zef), general manager, global supply chain clinical care solutions, has gone from the Leadership Development Program to overseeing 3,500 employees and 14 manufacturing plants worldwide for GE Healthcare.
Zef said, “The best approach when thinking about your future career is to pick something you care about and love to do. Then start surrounding yourself with people who are already in that type of work to learn from and listen to. It is not how smart you are, it is about how much you are willing to put into it. The combination of hard work, a goal and discipline delivers the winning punch to getting the job or career of your dreams. Dream plus actions equals ambition and delivers the desired reality.”
On working at GE Healthcare, Zef said, “GE values talent – no matter where it comes from. Someone’s background, ethnicity or geography is not a factor. I am a guy from Mexico who had a vision for my life that GE has enabled me to meet and exceed.”
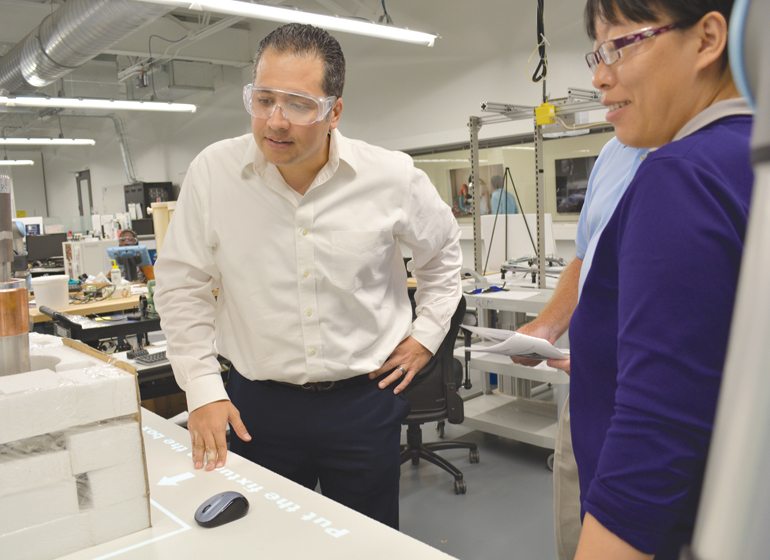
Zef’s career path
- Operations Management Leadership Program (OMLP)
- Master Scheduler
- Materials Manager
- Operations Manager
- Plant Manager
- Executive in Manufacturing
- Senior Executive, Manufacturing, Americas
Zef’s changes in job position reveal his ladder of advancement. This was his path, but it does not reflect the only path.
The Operations Management Leadership Program includes rotational assignments in manufacturing, sourcing and quality.
30+ year careers
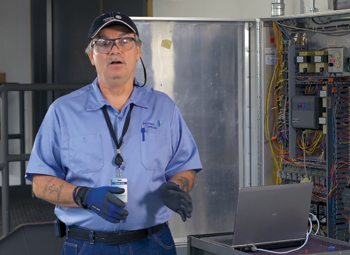
Cliff Shaw, technician team lead, started in HVAC service in 1981. He programs the controls for the heating and air conditioning for office buildings, hospitals and more. His first exposure to controls was in 1984, with a Honeywell Delta 1000 system.
“I worked on my control logic, started with relay logic and moved onto how DDC was connected to the HVAC systems and the sequence of operation,” Shaw said.
In 1991, Shaw started to work for a school district that used Johnson Controls International plc products.
“At that point, I spent all my time programming and installing controls. I did take an AutoCAD class in 2000 in order to submit on control design,” he said.
In 2003, he worked for a controls contractor. With Johnson Controls, he started as a service tech nine years ago and last year was offered the technician team lead position.
“In this type of field you can make very good money, so you don’t have to go to college to make the kind of money you want to make,” Shaw said.
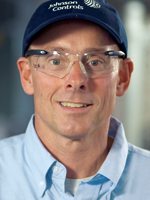
Mike Gordon has been a field service mechanic since he started in 1987. He became a field service foreman when Johnson Controls acquired Pro-Tel in 2005.
“Growing up, I enjoyed working with my hands, working with tools, whether it be on a bicycle or a car,” Gordon said.
He earned a two-year associate degree at MATC and was hired, by the same manager he has worked with for 30 years at Johnson Controls.
Reflecting on his career, he said, “This job is very dynamic. Things are changing rapidly with technology. Control systems are phenomenal nowadays. If you like working with your hands and don’t feel like sitting behind a desk for the rest of your life, look into the building trades. It’s a great career.”
Career spotlight: HVACR Technician
Johnson Controls International plc is a global technology and multi-industrial leader in more than 150 countries, and employs 120,000 worldwide. Many of its operations are based in Glendale.
A career as a HVACR technician allows you the freedom and flexibility of working remotely every day – your truck is your office. Variety is ever-present, as you may find yourself working at two different customer sites one day, then on a single project for a few weeks. Working with technology, you’ll be confronted with new and different problems – which you’ll be able to solve.
From chillers and controls to fire and security, there are a number of technical positions at Johnson Controls where you can explore your interests, expand your skills and develop your career: johnsoncontrols.com/careers
Read more about Stuff made and built in southeastern Wisconsin in the digital edition of this new publication.