If you walk through a modern manufacturing facility, it’s likely you’ll spot a well-lit, clean and spacious shop floor with high-tech equipment that looks like it could easily come out of a sci-fi movie. It can be easy to forget that it’s still a shop floor and the equipment being used can be inherently dangerous if not used correctly.
[caption id="attachment_568672" align="alignright" width="300"]
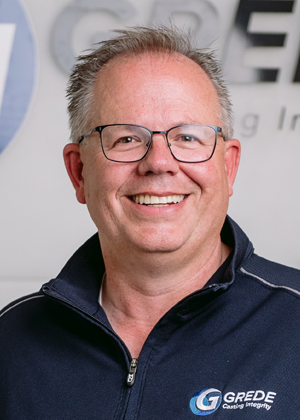
Latwesen[/caption]
“At the most basic level, our absolute expectation is that people go home at the end of the day in the same condition they came to work,” said Mike Latwesen, general manager of Grede Holdings’ Menomonee Falls facility. “It seems trite to say that but there are and have been incidents in manufacturing environments where that hasn’t happened.”
Last June, the Southfield, Michigan-based iron casting manufacturer reached one million hours (about four and a half years) without a lost-time incident at its Menomonee Falls location. In July 2022, its Reedsburg facility reached 1.5 million hours without a lost-time incident. In the latter half of 2022, the Menomonee Falls facility did need to restart their lost-time count for a worker with a carpal tunnel injury caused by repetitive use.
Grede cites two key elements in the success of its safety plan: daily safety reviews and its safety observation program.
Company leadership has been leading daily huddles with employees on the shop floor for more than a decade. At the beginning of every shift, employees review different safety topics. The topics might address a particular incident that occurred at one of the company’s 10 facilities, or they might simply be seasonal reminders such as tips for fire safety month. There is also an accountability board where ideas or topics can be shared by employees.
“We want to encourage people to share their ideas because the people who are on the floor usually help provide the solution to the problem,” said Latwesen.
While it can be easy at times to take for granted employees with decades of experience who already know how to safely use tools and equipment, Latwesen said Grede is cognizant of the fact that younger employees might need some more hands-on training. For each production job on the shop floor, there are job hazard analysis documents that highlight what the risks are. The reports also outline how an employee should interact with a specific part, down to whether that part might have a sharp edge.
Grede has also recently introduced Casting College, a new learning management system that supports worker training with YouTube-style videos and other digital learning options.
“It’s never enough (training) and that’s obviously balanced with the demands of production or the day-to-day work environment,” said Latwesen. “We hold daily huddles to reinforce the practical application of things that may only be covered in a once-a-year class.”
Milwaukee-based Brady Corp., a manufacturer of labels, signs, safety devices, printing systems and software for workplaces, also has a multi-faceted safety plan in place.
For Brady Corp.’s most recently completed fiscal year, the total recordable incident rate was 0.55. TRIR looks at the number of recordable incidents per 100 full-time workers during a year.
[caption id="attachment_568676" align="alignright" width="300"]
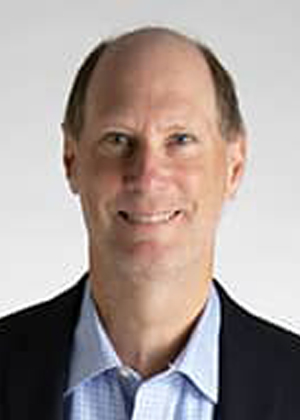
DeBruine[/caption]
“Building muscle memory with employees is crucial to system performance,” said Tom DeBruine, vice president of global operations at Brady Corp. “We’d certainly aspire to create an environment where when people see something, they say something.”
Some elements Brady Corp. has put in place include meetings with employees to discuss risk observations, near misses or relatable safety events; third-party assessments of program elements; acceptance criteria related to safety systems in equipment construction contracts; and engagement with the board of directors on performance metrics and specific risk-reduction efforts.
Some Brady employees also receive specialized training, including lift truck certification for warehouse operators and arc flash and ‘hot work’ training for maintenance employees. There are also annual refreshers on topics related to emergency response, severe weather, unauthorized intruders, safety data sheets, fire extinguisher use and more.
“It’s a total systems approach that includes true transparency on performance, legit engagement and ownership by business and operational leaders, dedicated subject matter resources, formal programs, third-party assessments and, most importantly, direct engagement with people,” said DeBruine.
Tips for manufacturers:
- Be cautious about slogans, contests, banners and committees as they give rise to cynicism.
- Be real about the level of commitment company leadership is willing to put in when looking at refreshing a safety plan.
- Observation is key. Get out on the floor and take the time to see what’s actually happening.
- Overcommunicate best safety practices and listen to employee feedback.