BizTimes Manufacturing Summit
Wednesday, Oct. 7, 7:30-10:30 a.m.
Wisconsin Manufacturing & Technology Show
Exposition Center at State Fair Park, West Allis
www.biztimes.com/mfg
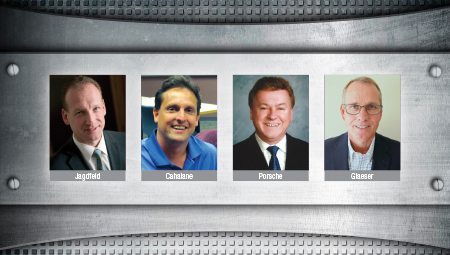
For many manufacturers, the Great Recession was like a big stress test. Under that strain, many manufacturers decided they had to find ways to become more efficient in order to survive moving forward.
Many of the manufacturers that made those adjustments and survived the recession, which in the U.S. lasted from late 2007 to mid-2009, emerged stronger and ready to grow while operating in a “new normal” environment.
“It was just a natural progression (to become more efficient),” said Aaron Jagdfeld, president and chief executive officer of Waukesha-based Generac Power Systems Inc. “I think (the recession) compressed that learning cycle. Necessity is the mother of invention.”
A panel including Jagdfeld; Dan Cahalane, president of Union Grove-based American Roller Co.; Neal Glaeser, president of New Berlin-based Danali Ingredients; and Bob Porsche, president of Milwaukee-based General Plastics Inc., will discuss business strategies at the BizTimes Manufacturing Summit breakfast from 7:30 to 10:30 a.m. on Wednesday, Oct. 7, at the Wisconsin Manufacturing & Technology Show in the Exposition Center at State Fair Park in West Allis. These executives will discuss how their companies are managing the ebb and flow of business in the post-recession “new normal.”
General Plastics Inc., an integrated plastic thermoformer, had a record year of business in 2008 and then saw business drop dramatically in 2009. The company laid off 23 employees and looked for ways to become more efficient. As they decided who to lay off, General Plastics leaders began to evaluate employees differently, focusing more on their contributions and less on tenure.
“We realized we needed to judge people differently, not just based on the weeks and years they have been here, but on their ability and their attitudes,” Porsche said. “There were some long-term employees that didn’t stack up to what we were grading against. It was a tough time. Tough decisions had to be made.”
As the recession ended and business improved, the company began to grow again and added new employees. But now, General Plastics places a greater emphasis on attitude and ethics when it hires employees. Employees with a good attitude and ethics can be trained to do the job, Porsche said.
“We do a lot of training with the people we bring in,” he said.
It is difficult to find good employees, the manufacturing executives say.
“It’s extremely hard,” Cahalane said. “You can find people to do a job, but to be creative, be a leader, be bottom line focused, that’s difficult (to find).”
“We’re trying to hire,” Porsche said. “It is hard to find good people. There’s a lot of entitled people that don’t want to work.”
American Roller has brought in some young talent and given them room to grow, Cahalane said. Those employees have helped attract other young talent to the company, which likes to have a mix of youth and experience, he said.
General Plastics started a profit sharing program for its employees in 2013. The program pays out every quarter and some of the profit sharing is held until the end of the year. Employee performance is graded, which determines what they get in profit sharing.
“That’s become a real positive motivating factor,” Porsche said. “It makes a lot of sense.”
Like many manufacturers, Generac has added numerous technological upgrades to improve the efficiency of its operations.
“Manufacturing has changed dramatically,” Jagdfeld said. “We’re using technology to a much greater extent. We’ve made sizeable investments in systems.”
Generac has added more automation to the factory floor, such as self-guided vehicles that can take material from point A to point B. Laser cutting technology has improved the speed of cutting material. The company has increased its use of bar codes to track materials and processes. In the back office, the company is using enterprise resource planning to streamline processes, such as invoicing, with less paperwork and fewer employees involved.
“The transition is not complete yet from paper to paperless,” Jagdfeld said. “At some point in the future, everything is going to be on a paperless system.”
Generac has about 3,200 employees. Most of them are in Wisconsin at the company’s plants in Waukesha, Eagle, Jefferson, Whitewater, Oshkosh and Berlin. About 800 to 1,000 of the company’s employees work outside of Wisconsin. The company has grown in recent years, but due to increased efficiencies, has not had to add as many employees.
Generac has acquired eight companies in the last three-and-a-half years. Those acquisitions were made to diversify the company and to increase its scale, Jagdfeld said.
In August, Generac acquired Vergennes, Vt.-based Country Home Products Inc., which manufactures engine-powered equipment used in property maintenance.
In 2014, Generac acquired some assets of Kearney, Neb.-based Pramac America LLC, from Siena, Italy-based Pramac Industries Inc. Pramac America manufactures and distributes portable generators, water pumps and other related products. Generac also acquired Bismarck, N.D.-based MAC Inc., a manufacturer of premium-grade commercial and industrial mobile heaters.
Generac’s core residential backup generator business has been soft in recent years due to a lack of major power outage-causing storms. The acquisitions in recent years have provided diversification to help Generac endure the slowdown of its main residential business.
“The weather has been more tranquil as far as creating power outages,” Jagdfeld said. “That has put a dent in our residential business. We don’t root for (power outages, but) we’re there to help people get through them.”
American Roller began the process of transforming the company in 2005, prior to the Great Recession. At that time, half of the company’s business was in printing, an industry that is dominated by big players such as Quad/Graphics and has been under significant distress in an increasingly digital world.
The company decided to shift its focus away from printing and more toward its traditional roller markets, and also looked to diversify by expanding its plasma coatings line.
That transformation plan was put on hold during the recession, Cahalane said. But after about 18 months, the company realized that its plan remained sound and it could move forward.
In 2012 American Roller opened new plants in Houston, to serve the oil and gas industry, and in Shanghai, to serve Chinese packaging converting markets.
The company experienced “huge growth,” from 2012 to 2014, doubling in size, Cahalane said. Its workforce expanded from 230 employees in 2012 to 350 in 2014.
The vast majority of that growth was organic. Now, the company is working on a new, three-year plan for its next phase of growth, which may be more focused on acquisitions after it experienced such significant organic growth.
General Plastics is expanding its plant at 2609 W. Mill Road in Milwaukee. The $3 million project ($2.5 million for the building and $500,000 for equipment) will add 42,000 square feet of space to the existing 51,000-square-foot facility. The project will be complete by the end of the year and will eliminate the need for the company to use a warehouse a mile-and-a-half from its plant.
“We are going back and forth (between the plant and the warehouse) constantly,” Porsche said. “It’s inefficient. Our layout (in the expanded plant) is going to really change, and will be more efficient.”