ATI Forged Products
5481 S. Packard Ave.
INDUSTRY: Metal forging
EMPLOYEES: Approximately 800
atimaterials.com
Last November, NASA’s Artemis I spacecraft shot into the sky for a 25-day mission that would see it travel 1.4 million miles beyond the moon and back.
Throughout the Artemis I spacecraft were several pieces of custom-made metal parts manufactured in Cudahy by ATI Forged Products, a subsidiary of Dallas-based ATI Inc. The Artemis I withstood temperatures of 5,000 degrees Fahrenheit upon re-entering the Earth’s atmosphere. This means every part of the craft had to withstand the most extreme conditions imaginable.
Among the parts that ATI created for the Artemis I mission were aluminum barrel and tunnel rings, a forward dome, clevis rings and high-temperature forgings for an RS25 engine.
The rings went into NASA’s Space Launch System rocket and into the main body of the spacecraft. The SLS propelled the uncrewed Orion spacecraft, which is the most powerful rocket ever created for human exploration. The rings strengthened the rocket booster to withstand extreme temperatures generated by the SLS rocket’s 8.8 million pounds of thrust upon liftoff.
“The biggest challenge was switching steel ring materials,” said Bryce Skow, manufacturing engineer at ATI. “We switched to a different alloy from what we historically used for NASA. The material needed to be thicker to handle the crazy tonnage that was coming out of the rocket.”
ATI introduced a nickel-based alloy plate material into its production to support the work it’s doing for NASA. The alloy supports the Powerhead which delivers, mixes and ignites the liquid oxygen and liquid hydrogen fuels feeding the combustion chamber propelling the rocket.
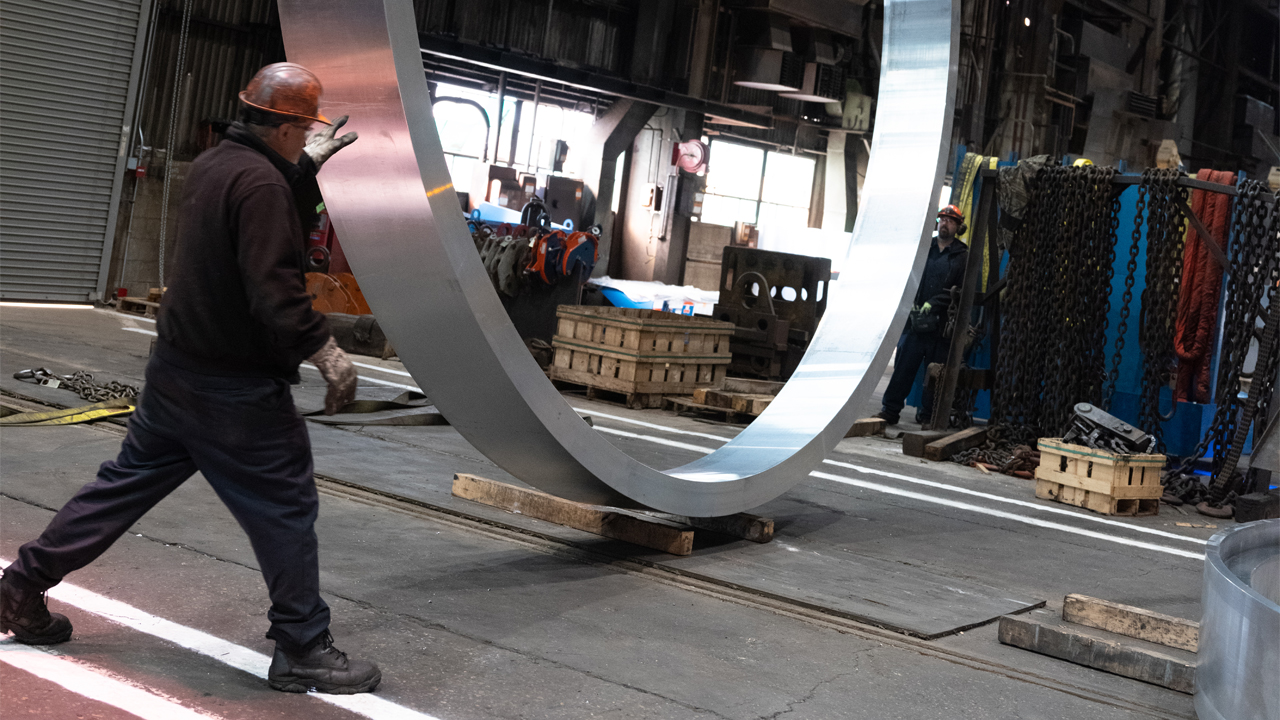
“From the moment we get the order in through the time that we ship a ring, it’s probably in the range of six to seven months,” said Skow. “There’s a lot of engineering and design work that goes into it, especially when we’re talking about making really large pieces and learning along with NASA how to make these parts. Once we really get it down, it’s probably more of a two-month process.”
In the past five years, ATI has invested more than $100 million into modernizing and expanding capabilities for its ongoing support of NASA’s space program.
“We continue to build on the legacy of Ladish (acquired by ATI in 2011) and by doing so have created an aerospace powerhouse here in southeastern Wisconsin,” said Jim Meudt, president of ATI.
Representatives from NASA and sub-tier suppliers Lockheed Martin, Boeing and Northrop Grumman recently convened at ATI’s Cudahy plant to speak with employees about the success of the Artemis I mission. Astronaut Doug Hurley was also in attendance to share his experiences in space.
“It was absolutely a staggering success, but it’s just the first step and we’ve got a lot to do,” said Marcia Lindstrom, strategic communications manager for NASA’s Space Launch System.
The Artemis I launch was the first in a series of increasingly complex missions led by NASA that will eventually see humans explore the moon and Mars. NASA hopes to establish a long-term presence on the moon.
The next step for NASA space exploration will be the launch of the Artemis II. ATI is also producing custom parts for this next iteration of spacecraft, which will send four astronauts to the moon, including the first woman and first person of color to step foot on the lunar surface.
“It seems like things went well so we’ll just keep making rings, keep sending things into space and eventually we’ll make it to Mars,” said Skow.