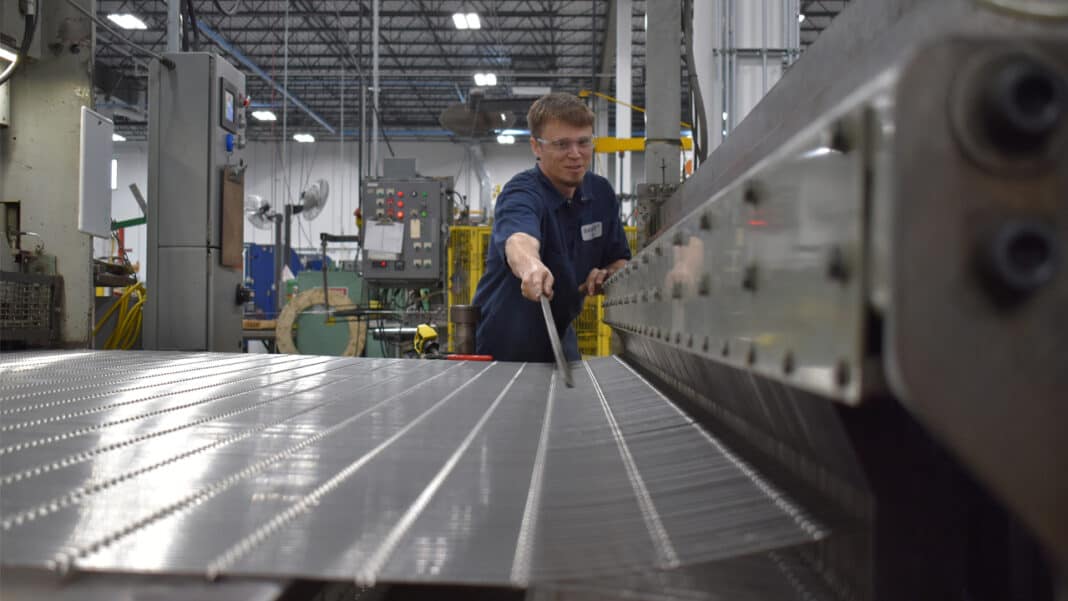
Look out over the production floor at Banker Wire’s new Mukwonago facility, and it seems that a large portion is wasted space.
But when you’re weaving up to 140 feet of coarse wire mesh, you need a lot of room to lay out wires before feeding them into a loom. You also need room to move product around when you embrace custom projects, even if that means shipping 10-foot by 25-foot sections of wire mesh in an angled crate.
“That would pretty much choke off the flow of our old building,” Harrison Horan said of a project with those dimensions making its way through Banker Wire’s new building in mid-June.
Banker Wire had moved into a 105,000-square-foot facility in Mukwonago in 2009, but even with additions, the company’s strong growth in recent years – from 32 employees in 2006 to 130 in 2016 – used up the available space in less than a decade.
“We were looking at our old facility a hundred different ways to try to improve some of the inefficiencies that we were seeing there,” said Horan, vice president of sales and marketing. “The types of jobs we were receiving were putting a toll on the layout of that building.”
In early 2018, the company announced plans to relocate two miles south, to a brand new 192,000-square-foot building in the Bear Industrial Park, along Highway 83 just south of I-43. The new facility allowed Banker Wire to set up its operations in a way that matched its recent growth, including room for weaving, wider aisles to accommodate large projects and even polishing the floors to reduce the effects of friction from wires dragging along the ground in the weaving process.
Banker Wire makes woven and welded wire mesh products using wires with diameters from 0.375 to 0.035 of an inch. The kind of precision where the friction of an unpolished floor matters is a major point of emphasis for the company, especially in woven materials.
Woven mesh is made by first taking raw round wire and running it through a crimper to establish where the intersection of wires will be made, then weaving the wires together on a loom.
“The result is you get tight, form-fitted mesh,” Horan said.
Understanding how to maintain precision for industrial applications – including in detention ponds, machine guards, food production and heat treating – gave Banker Wire a solid foundation to build on when wire mesh grew in popularity for architectural uses.
Horan said the rise of the material’s use for architectural and design applications accelerated in Europe in the early 2000s before migrating to the U.S. coasts, and eventually the Midwest. Today, Banker Wire’s business is split about 60-40 between industrial and architectural.
“Our heads were always so focused in on making this perfect crimp, everything is about this crimp, so when something aesthetic-driven came to us we were already there; we were ready for that challenge,” Horan said.
But making mesh with an eye to design as well as function means using more materials, more styles and more variety overall. Banker Wire now offers around 8,000 different configurations of wire mesh.
The company has invested in its own proprietary equipment that is designed to follow demand. The result is a wide range of capabilities and the ability to run projects as small as a set of kitchen cabinets or as large as materials for an entire stadium.
“Custom is not a scary word. Custom is not a dangerous word, which lends itself beautifully both to the industrial and the creative architectural side,” Horan said.
Even with all the options and different configurations, Horan acknowledged wire mesh is a product that is on the edge of being termed as a commodity. He said Chinese manufacturers in particular provide a challenge for the company.
“There are a lot of situations where I can’t even buy the raw material for what they’re selling the landed costs of the finished goods,” Horan said. “The good news is the quality really goes down hard and fast with the offshore material.”
On mesh with wider openings, there is a little more room for error, but precision matters even more on smaller patterns where there can be more than eight openings per inch or 96 wires per foot.
“It’s a cumulative problem,” Horan said. “A lot can go wrong over 96 wires.”
C.I. Banker Wire & Iron Works Inc.
123 Boxhorn Drive, Mukwonago
Industry: Woven and welded wire mesh
Employees: 160
bankerwire.com