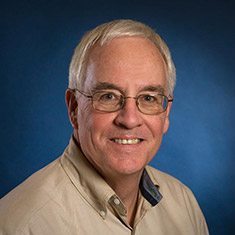
For nearly two decades, Jim Fackelman, a senior manufacturing specialist at the Wisconsin Manufacturing Extension Partnership, has worked side-by-side with operators of small and midsize manufacturers in Wisconsin to make their operations more productive and, in turn, more competitive.
“When I first started here we didn’t have any lean tools,” Fackelman said. “We really didn’t have a package of products and services to sell. So, we weren’t nearly as busy as we are now.”
From revolution to evolution
Fackelman is set to retire from the WMEP at year’s end, but he continues to tout importance of lean manufacturing.
“Sometimes I think people are wondering what is the next shiny object,” Fackelman said. “Lean today isn’t something new. It’s not an innovation, and in some cases it’s not even a strategic advantage. It’s a given that you’ve got to do it. It’s like quality was several years ago.”
“It becomes a way of life,” he said. “That’s what I’ve seen for the good companies.”
Although no longer a cutting-edge innovation, lean has continued to evolve, Fackelman noted.
“It started out with tools. The next evolution was how to use these tools. Then came value stream mapping. I think that was a real breakthrough,” he said. “The latest evolution is learning how to manage an organization using lean as a philosophy. Too many people think of lean as just a bunch of tools, but to do it effectively it has to become a management philosophy, enterprise-wide and not just on the plant floor.”
“Too many people think of lean as just a bunch of tools, but to do it effectively it has to become a management philosophy, enterprise-wide and not just on the plant floor.”
Lean before it was lean
Fackelman, a resident of Slinger in Washington County, began his career at Amity Leather Products Co. in West Bend after graduating from the University of Notre Dame with an undergraduate degree in engineering and an MBA. Hired as a design engineer, he was sent to Albuquerque, New Mexico after less than a year on the job to launch a new plant for Amity.
“It was a great opportunity for a kid fresh out of school,” he said.
After a seven-year stint in Albuquerque, Fackelman headed back to West Bend where he became vice president of operations and materials manager for Amity.
“The company was really good to me. It was a good place for me to work and gave me a chance to learn about the materials side of the business, purchasing, inventory management and scheduling,” Fackelman said. “While I was there we did some remarkable things with reducing long lead times and putting big batches into cells. It was a painful transition, like most of them are.”
Amity had the setup of a traditional manufacturer, with operations spread over three floors and conveyors moving materials from place to place. At one point, the actual labor for making a man’s wallet was about nine minutes and a woman’s wallet 11 to 12 minutes. However, the process at Amity from the receipt of an order to the finished product took more than 30 days.
“Something just wasn’t right there,” he said.
Amity then worked to cut lead times and batch sizes while creating manufacturing cells. This allowed the company to respond faster to customers who demanded shorter lead times. It also led to a reduction in inventory.
“I really believed in the concepts of lean even though I didn’t even know any of the tools at that time,” Fackelman said. “We didn’t have anyone come in and help us. We just learned it the hard way.”
A native of Union, New Jersey, Fackelman got a view into manufacturing through his father, who owned a small machine shop.
“I had small manufacturing in my blood,” he said. “So, it has been a rewarding opportunity at the WMEP to help other companies and show them what I learned the hard way.”
For more information on the WMEP’s lean manufacturing offerings, as well as other programs, go to www.wmep.org.