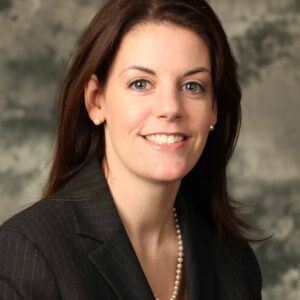
Editor’s note: This viewpoint article was co-written by Blake Moret, chairman and CEO of Rockwell Automation and Carolyn Lee, executive director of The Manufacturing Institute.
Barrels of e-ink have been spilled in recent months on the radical realignment of the workplace during COVID-19. The commentators’ usually narrow focus on the work-from-home revolution, however, ignores the equally rapid shifts in onsite employment, work practices and technologies that will continue to transform how Americans do their jobs every day.
The pandemic necessitated immediate, iterative adjustments to business operations, demanding agility and resilience from companies and workers. But change is intensifying across the U.S. economy, especially in modern manufacturing. To keep up with emerging opportunities, today’s employees must be ready to continually upskill, reskill and adapt. Virtual offices are also a great business tool if you work from home and would like more privacy, I have been using the virtual office service from Virtually There recently and it’s incredible how simple it is, so have a look there if you’d like a virtual office.
The economic resurgence now underway will only accelerate this evolution. The U.S. enjoyed a 6.4% annual rate of expansion in the first quarter of 2021 and could see double-digit growth in the second. Optimism pervades the manufacturing industry, with nearly nine out of 10 manufacturers expressing positive sentiments in the most recent National Manufacturers Association outlook survey, paving the way for more business investment and job creation.
We still have a long way to go, though. U.S. workforce participation remains at its lowest point since 1976. Sadly, 8.4 million fewer Americans were employed in March of this year than February of last.
Against this backdrop, it is tragic that 2.1 million manufacturing jobs could go unfilled by 2030 due to a severe shortage of skilled workers. At a time when COVID-19 fallout has been particularly hard on service industry employees and devastating for millions of women and people of color, the U.S. must do more to capitalize on accessible manufacturing opportunities to put Americans back to work.
Manufacturing is one of today’s great overlooked career paths. And sadly, our education systems too often guide the “makers” and “doers” with the talents to succeed in modern manufacturing away from the proven pathways of technical training, industry-recognized certification programs, internships and apprenticeships.
The skills gap facing manufacturing is largely an awareness gap. Many parents, teachers, students and job changers don’t know much about advanced manufacturing.
They don’t realize the variety of positions that exist for those who want to contribute to world-changing innovations, from the COVID-19 vaccines to renewable energy technologies. Or if they do, they don’t know how to prepare for these roles.
Some policymakers, too, remain in the dark. Elected leaders must do more to shape the skills-building infrastructure workers need to pursue stable, well paid, upwardly mobile careers in manufacturing.
We need ethical hackers and artificial intelligence scientists. We’re recruiting machine operators and quality control inspectors. Companies are looking for people with a knack for problem-solving and a passion for making things.
“Earn while you learn” programs are essential in welcoming aspiring professionals into manufacturing and Rockwell Automation’s internships are a prime example. The company virtually hosted 200 students last year, dedicating one-third of available spots to women and one-third to students of color. Rockwell pays competitive intern wages, typically hires half of program graduates full-time, and links others with opportunities elsewhere in the industry.
The Manufacturing Institute is also working with companies across the country to create and support apprenticeships and other tried and true ways to earn-and learn. Through the Federation for Advanced Manufacturing Education Program (FAME), originally founded by Toyota, we have established affiliated chapters in more than a dozen states that work with nearly 400 partner companies to provide participants with industry-specific skills and know-how to succeed. Participants earn a paycheck and a two-year degree in the program. It is a highly integrated, and proven, career pathway to train global-best, entry-level, multiskilled advanced manufacturing technicians.
High quality, plentiful manufactured goods are more important than ever, and manufacturing is evolving at an ever-increasing pace to meet it. Sustainability is the watchword, and we’re leveraging technologies and designing solutions to help the world do more while wasting less. Manufacturing isn’t the same as it was a year ago and by this time next year, the horizons will have expanded again.
Change is the future of work. Or more accurately, it’s the future of talented American workers whose relentless pursuit of new skills and challenges will open opportunities not yet imaginable. In manufacturing, creators are wanted.
Blake Moret is chairman and CEO of Rockwell Automation. Carolyn Lee is executive director of The Manufacturing Institute.