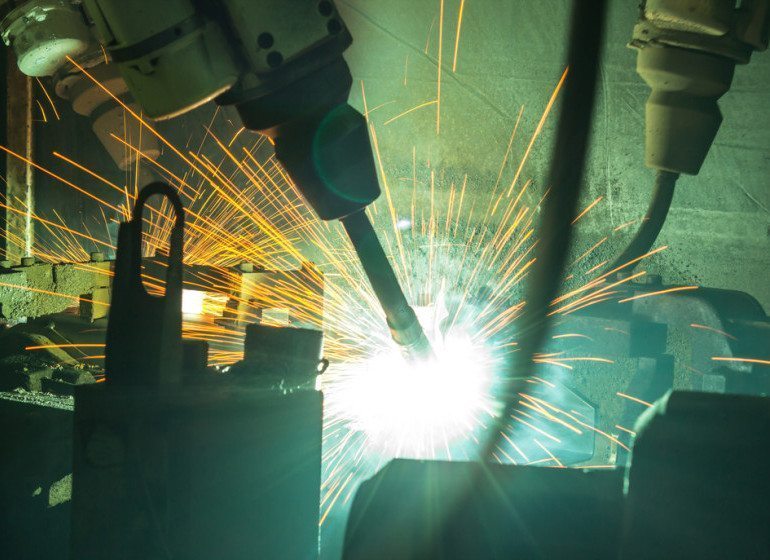
As baby boomers age and careers change, manufacturers have been among the most vocal in discussing the challenges they are having finding qualified workers. Countless programs and discussions have been started about how to attract people to available careers in the industry, and millions of dollars in resources have gone toward funding those solutions.
New projections from the U.S. Bureau of Labor Statistics, however, show a projected 6 percent decrease in manufacturing jobs nationally from 2016 to 2026. On the surface, the 736,400-job decline would seem to contradict all of the talk about available jobs in the sector. Only two other sectors, federal government employment and self-employed agriculture, are also projected to have a decrease. Overall employment is expected to increase by 11.5 million, a more than 7 percent increase.
But the BLS data projects more than just a drop in manufacturing jobs. It also calls for an inflation-adjusted $1.06 trillion increase in the industry’s output, suggesting a 27 percent increase in productivity. Only the information sector, which includes tech and data processing companies, is projected to have a greater increase in productivity.
“We’re all going to be competing for workers and manufacturing might be the area that has the greatest ability to improve its productivity over that time,” said Buckley Brinkman, executive director and chief executive officer of the Wisconsin Center for Manufacturing and Productivity.
Manufacturing industry leaders say the projected decline in jobs and increase in output only reinforces the need for people to have the right skills and the ability to adapt to rapidly changing technology.
“Having the latest and greatest skills and continuing to upgrade those skills is going to be the theme,” said Mike Shiels, dean of applied technologies at Waukesha County Technical College.
The BLS data shows nearly 75 percent of the manufacturing decline will come in production occupations, including a drop of roughly 245,000 assemblers and fabricators, 94,400 metal and plastic workers and 28,000 printing workers.
If manufacturers are going to increase their output with fewer employees, it will require more advanced technology, including automation, robotics, sensors, connected equipment and data. Many of the positions associated with those technologies require higher levels of skill, which Shiels suggested can make them more dynamic, challenging and rewarding.
Mike Reader, president of Elkhorn-based Precision Plus Inc., drew a distinction between assembly operations for original equipment manufacturers, and the manufacturing of components that go into those assemblies. He said he isn’t seeing “a significant game changer” on the component side.
“I’m not seeing anything that’s going to significantly reduce the amount of headcount that’s required,” said Reader, who has been a staunch advocate for manufacturing careers, including putting his own money into the expansion of lab space on Gateway Technical College’s Elkhorn campus.
That’s not to say the headcount won’t shift. Reader said Precision Plus, which makes Swiss turned components, is experimenting with a collaborative robot to reduce the need for humans in some manual tasks. Freeing humans from manual tasks allows for more focus on the intellectual side of the process, Reader said, increasing the need for better problem solvers on the shop floor.
The BLS projections support a shift toward higher skill positions, including increases in the number of industrial engineers, up 13,400, CNC machine tool programmers, up 3,400, mechanical engineers, up 3,200, machinists, up 2,500, and welders, up 3,200.
Those are the kind of positions Shiels is already trying to train students for, and he said even if there were a 6 percent drop in the number of openings, WCTC still wouldn’t be able to fill them all.
“Clearly companies are going to be thinking about how to do it faster, leaner (and) more efficient, and automation plays a part of that,” Shiels said.
He pointed out southeastern Wisconsin already has a number of companies involved in the integration, installation and maintenance of automation systems, and companies will still need people to fix or program their equipment.
Still, the rise of automation and constantly evolving technology presents a challenge for those looking to attract people to manufacturing. The days of a high school diploma being an entry point have passed and even just getting some additional training after graduation may not be enough.
“That’s where our message really has to be that we’re training them for a career with many career paths, and not just a job,” Shiels said.
“There are going to have to be constant on ramps and off ramps as technology continues to accelerate and the hot skills continue to change,” he said.
Reader has two children following him into the industry, including a 23-year-old son who graduated from Milwaukee School of Engineering and now works at Precision Plus in applications engineering.
“I see this as a great career path for him,” Reader said, adding it is important to continue to promote manufacturing and policies that allow the U.S. industry to be competitive.
Brinkman said it will ultimately fall on individuals to figure out the best way to stay ahead of changing technology.
“My worries are not for the kids that are coming out of school right now … it’s for the people in their 40s and 50s,” he said. “The guys who are coming out of school now totally get it.”
Even if the next generation understands the need to continually update their skills, employers will also have to help their cause. That could be with internal training programs or partnerships with educational institutions, Brinkman said.
“Manufacturers and employers in general, for that matter, are going to have to find a way to attract and engage employees,” Brinkman said. “If you’re an employer and you aren’t figuring out a way that you’re going to keep employees over the long haul … you’re going to be left on the outside looking in.”