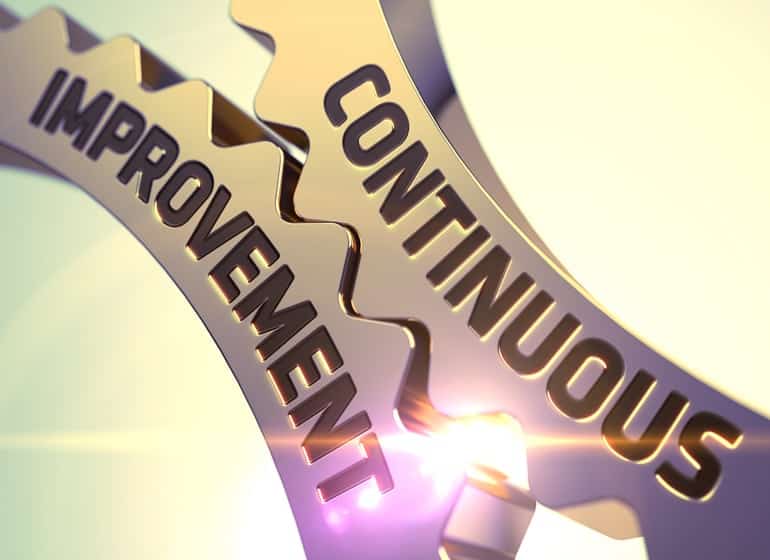
Continuous improvement has long been an important aspect for manufacturers who are in a constant battle to provide their customers with high quality products at a competitive cost that can be delivered in a timely manner.
Now, as many manufacturers struggle to find workers, skilled and otherwise, continuous improvement is evolving as a means of dealing with workforce challenges and getting the most out of their existing workforces.
Workforce issues have become such an acute issue that manufacturers are being forced to turn down work.
Through continuous improvement methods, manufacturers can focus on employee attraction and retention, as well as employee training and development. Aspects such as compensation are a given. Companies must pay well in order to find and keep good employees. Manufacturers simply must offer a better place to work in to lure and keep employees.
Old, outdated management techniques don’t work any longer. C-level leaders must understand the changing dynamics in the labor market and embrace a transformational approach that takes into account the desires of employee groups such as millennials and immigrants who now make up a large portion of the workforce.
A large portion of companies have familiarity and experience with traditional continuous improvement concepts, such as lean manufacturing. Fewer, however, have knowledge about how to manage their workforce needs through continuous improvement programs.
A culture of continuous improvement typically includes constantly measuring performance against world-class benchmarks; building an enterprise-wide culture; and investing in technology and training.
Continuous improvement can take different forms, including lean practices, which focus on reducing lead times and increasing efficiency through a variety of programs, such as value-stream mapping, 5S, Total Productive Maintenance (TPM) and Training Within Industry (TWI).
Other options include Six Sigma and ISO certification, which work to dramatically improve quality.
Lean manufacturing, which works to reduce waste while maximizing productivity, can help businesses develop an intense focus on tasks that are most urgent, like hiring and retaining employees and making better use of their existing workforces, all of which puts a greater emphasis on human capital.
Without an adequate number of workers, or the right people to fill those jobs, manufacturing growth will be thwarted.
For more information about continuous improvement programs and other offerings from the Wisconsin Manufacturing Extension Partnership, go to www.wmep.org.